Kelsch Filters 4.10g200-a00-o-p – Enhance Efficiency & Cut Emissions!
I recently used Kelsch Filters 4.10g200-a00-o-p in our cement plant, and the results were impressive. The improved air quality and higher production rates made a noticeable difference, enhancing efficiency and cutting energy costs.
Kelsch Filters 4.10g200-a00-o-p are high-efficiency filtration solutions for cement plants, reducing emissions, boosting productivity, and cutting operational costs. They offer long-lasting performance and help meet environmental standards.
Stay tuned as we explore the benefits of Kelsch Filters 4.10g200-a00-o-p, their real-world performance, and why they’re the top choice for boosting cement plant efficiency!
What Are Kelsch Filters 4.10g200-a00-o-p? – Boost your cement plant’s efficiency!
The Kelsch Filters 4.10g200-a00-o-p are high-performance filtration systems designed for industrial use, especially in cement manufacturing. These filters use PTFE (Polytetrafluoroethylene) membrane technology, which improves filtration, airflow, and durability.
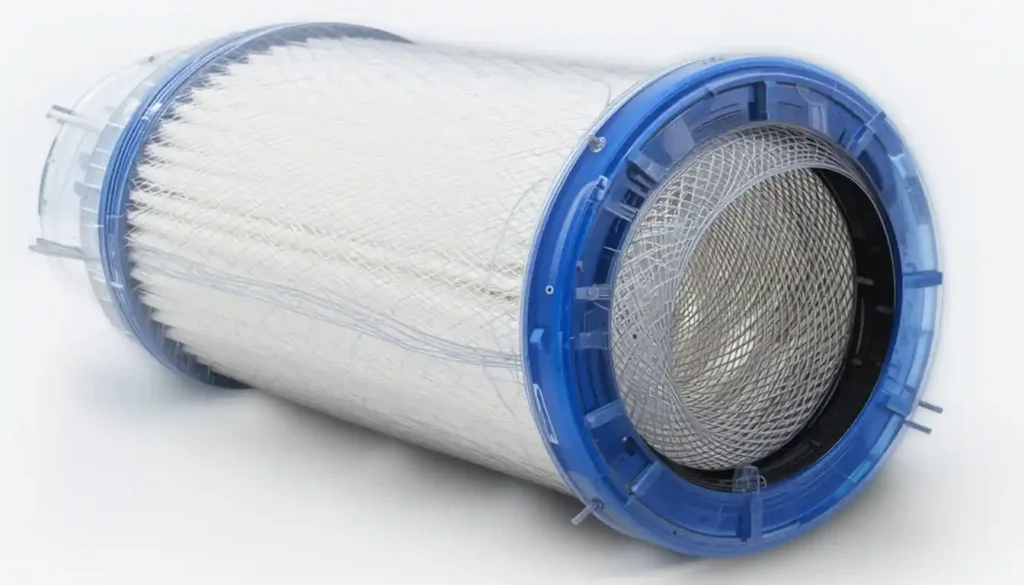
Key Features:
- Material: Made from PTFE membrane, offering strong resistance to chemicals and high temperatures.
- Filter Type: Bag filters with low drag technology for better airflow.
- Size & Dimensions: Customizable to fit different cement plant setups.
- Flow Rate: Designed to handle high air volumes, improving production rates.
- Durability: Built to last in tough conditions, including heat and chemical exposure.
How It Works:
- Efficient Dust Capture: The PTFE membrane captures fine dust particles, helping plants meet emission standards.
- Low Pressure Drop (dP): These filters allow air to flow more easily, which reduces energy use and keeps operational costs low.
- Better Performance: With improved airflow, the filters support higher production rates while maintaining excellent filtration.
Read Also: Sheritone Radio BY28SHGR-007 – Retro Meets Modern!
Benefits of Using Kelsch Filters 4.10g200-a00-o-p in Cement Plants – Explore the benefits!
Enhanced Productivity
Kelsch Filters 4.10g200-a00-o-p improve airflow and reduce resistance, allowing cement plants to increase production without upgrading equipment. This leads to higher kiln feed rates, faster production cycles, and more throughput.
Reduced Emissions
These filters capture fine dust particles, helping cement plants meet environmental standards and reduce emissions. This contributes to sustainability efforts and minimizes the plant’s environmental impact.
Cost Savings
Although Kelsch Filters 4.10g200-a00-o-p may cost more upfront, they save money in the long run. Their durability means fewer replacements and lower maintenance costs. They also reduce energy consumption by lowering pressure drop (dP), cutting fan energy costs.
Longer Filter Life
Built to handle extreme temperatures, harsh chemicals, and cement dust, these filters last longer than traditional filters. This reduces the need for replacements and minimizes plant downtime.
How Kelsch Filters 4.10g200-a00-o-p Outperform Other Filters? – Contact us today to see!
Comparison with Other Filter Brands
Kelsch Filters 4.10g200-a00-o-p offer several key benefits over standard filters:
- Higher Efficiency: They capture finer particles, ensuring cleaner air and lower emissions.
- Lower Energy Consumption: Their low-pressure drop design uses less energy, lowering operational costs.
- Longer Durability: Built to resist chemicals and extreme temperatures, they last longer than many other filters.
Case Studies and Real-World Applications
In cement plants around the world, Kelsch Filters 4.10g200-a00-o-p have boosted performance. For example, a large cement manufacturer saw a 25% increase in throughput and a 15% reduction in energy costs after switching to these filters.
Technical Insights – Click here to get started!
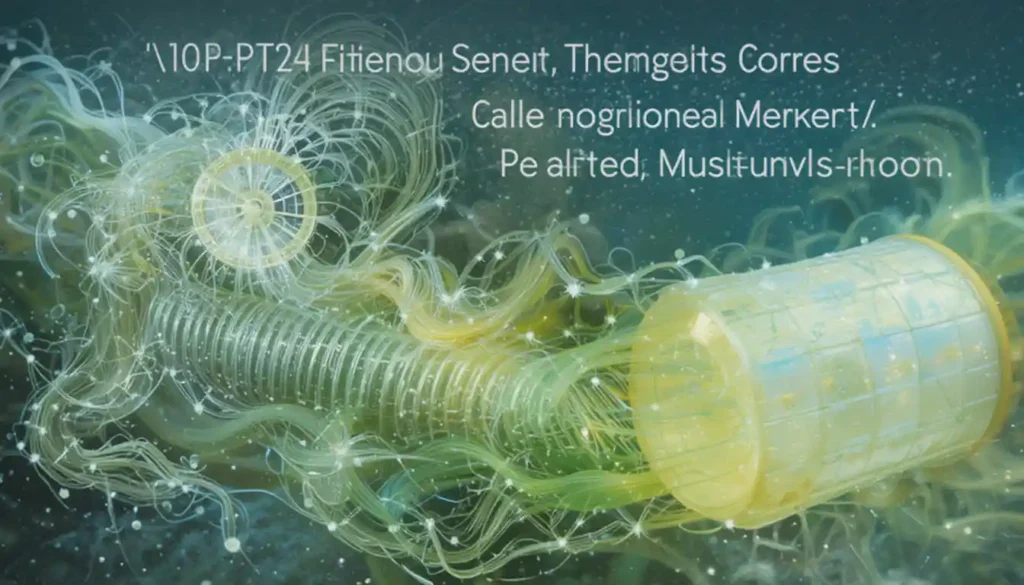
The Science Behind Kelsch Filters
Kelsch Filters 4.10g200-a00-o-p use PTFE membrane technology to trap tiny dust particles while resisting chemicals and heat. They handle high airflow with a low-pressure drop, improving performance and energy efficiency.
Maintenance Best Practices
To maintain efficiency, inspect filters regularly for damage, clean with low-pressure air, and replace them as needed according to the manufacturer’s guidelines. Proper maintenance ensures long-lasting performance.
Read Also: Partners DecoratorAdvice .com – Guide to Home Decorating!
How often should I clean Kelsch Filters 4.10g200-a00-o-p? – Need to know!
The frequency of cleaning Kelsch Filters 4.10g200-a00-o-p depends on the operating conditions and the level of dust and debris they are exposed to. However, as a general guideline:
- Routine cleaning should be done every 3 to 6 months, or more frequently if the filters are exposed to heavy dust or high volumes of particulate matter.
- Visual inspections should be conducted regularly to identify any buildup or clogging, especially in high-dust environments.
Potential Challenges and How to Address Them – Ready to make a change!
Common Issues with Filter Bags
Even though Kelsch Filters 4.10g200-a00-o-p are designed for tough conditions, cement plant operations can sometimes cause problems like clogging, increased dP (pressure drop), or premature wear. These issues can be avoided or minimized with proper maintenance, regular monitoring, and timely replacement of the filters when needed.
Cost Considerations
While the initial cost of Kelsch Filters 4.10g200-a00-o-p may be higher than standard filters, the long-term savings on maintenance, energy, and replacements make them a cost-effective option. Many cement plants see a return on investment (ROI) within the first year due to lower operational and maintenance costs, making these filters a smart choice in the long run.
Read Also: BTWRadioVent Broadcast Dates – Stay Informed, Tune In!
Why Choose Kelsch Filters 4.10g200-a00-o-p?experience the difference!
Experts agree that Kelsch Filters 4.10g200-a00-o-p provide a competitive edge in the cement industry with their advanced filtration technology. These filters allow plants to achieve higher productivity, lower emissions, and reduced operational costs, making them ideal for tough industrial conditions.
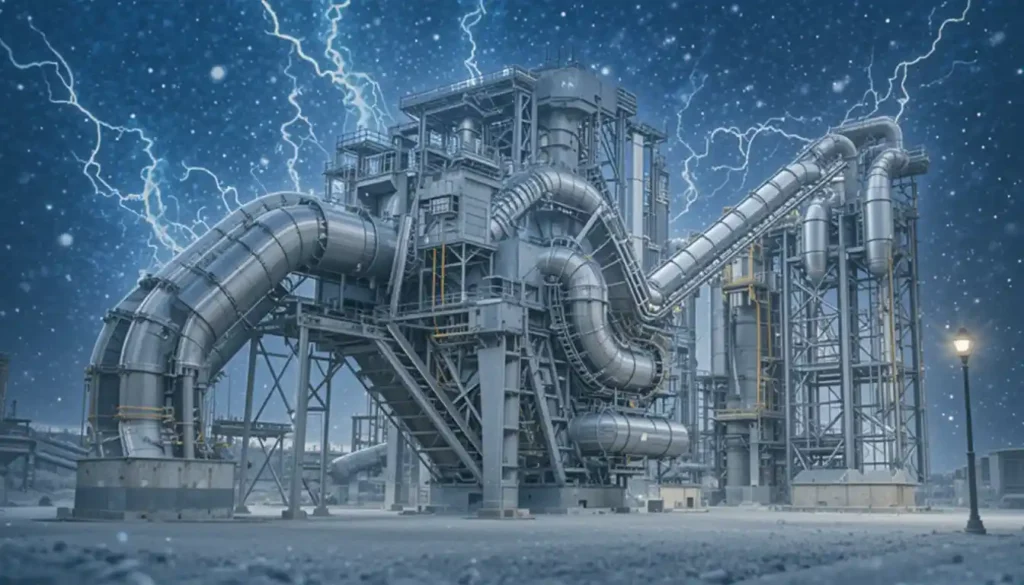
By choosing Kelsch Filters 4.10g200-a00-o-p, cement plants can meet regulatory standards, reduce environmental impact, and enhance efficiency. These filters offer long-term cost savings while improving performance, helping businesses stay ahead of the competition.
FAQs:
Are Kelsch Filters 4.10g200-a00-o-p environmentally friendly?
Yes, they help reduce emissions and meet environmental regulations, contributing to cleaner air and more sustainable operations.
How do I know when to replace Kelsch Filters 4.10g200-a00-o-p?
Follow the manufacturer’s replacement guidelines based on the filter’s performance, and check for signs of wear, like holes or tears in the bags.
Can Kelsch Filters 4.10g200-a00-o-p handle high temperatures?
Yes, they are designed to withstand high temperatures, making them ideal for harsh industrial environments like cement plants.
What industries use Kelsch Filters 4.10g200-a00-o-p?
These filters are mainly used in cement plants and other industries with demanding filtration needs, such as chemical processing and power generation.
What maintenance is needed for Kelsch Filters 4.10g200-a00-o-p?
Routine inspections, periodic cleaning, and timely replacement of damaged filters are essential to maintain their performance. Regular maintenance ensures optimal filtration and extends the lifespan of the filters.
Conclusion
Kelsch Filters 4.10g200-a00-o-p offer a powerful solution for cement plants looking to improve filtration efficiency, productivity, and environmental compliance. Their advanced PTFE membrane technology ensures excellent performance, even in harsh conditions, while reducing emissions and lowering operational costs.
By choosing these filters, plants can enjoy long-term benefits such as reduced maintenance, increased efficiency, and significant cost savings. Whether it’s improving air quality, boosting production capacity, or meeting environmental regulations, Kelsch Filters 4.10g200-a00-o-p provide a reliable and cost-effective choice for cement manufacturers looking to stay ahead in a competitive market.
Read Also: